top of page
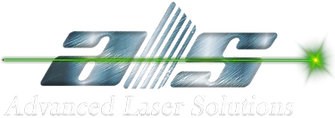

Frequently Asked Questions
-
What is laser technology?Laser technology is a branch of physics that deals with the generation, amplification, and application of light waves through a process called stimulated emission. Lasers produce a highly focused, monochromatic, and coherent beam of light, making them incredibly versatile tools with applications in various fields.
-
How does laser technology work?Laser technology relies on the principle of stimulated emission, where excited atoms in a gain medium are stimulated to emit photons of the same wavelength and phase as an incoming photon. This process amplifies the light, creating a coherent beam. The laser cavity, a resonant chamber, ensures that only light of a specific wavelength and direction is amplified, resulting in a highly focused and directional beam.
-
What are the different types of lasers?Lasers are classified based on their gain medium, wavelength, and operating mode. Some common types include: Gas Lasers: Use a gas as the gain medium, such as helium-neon (HeNe) or carbon dioxide (CO2) lasers. Solid-State Lasers: Use a solid material as the gain medium, such as neodymium-doped yttrium aluminum garnet (Nd:YAG) or titanium-sapphire (Ti:Sapphire) lasers. Dye Lasers: Use organic dye molecules dissolved in a solvent as the gain medium, offering tunable wavelengths. Semiconductor Lasers: Use a semiconductor material as the gain medium, commonly found in laser pointers and optical drives. Fiber Lasers: Use an optical fiber as the gain medium, offering high power and efficiency.
-
What are the applications of laser technology?Laser technology has revolutionized various fields, with applications ranging from scientific research to everyday life. Some key applications include: Manufacturing: Laser cutting, welding, marking, and engraving. Medicine: Laser surgery, laser therapy, and medical imaging. Communications: Fiber optic communication, laser pointers, and barcode scanners. Scientific Research: Spectroscopy, microscopy, and holography. Entertainment: Laser shows, laser displays, and laser pointers. Military: Laser guidance systems, laser rangefinders, and laser weapons.
-
What are the advantages of using laser technology?Laser technology offers numerous advantages, including: High Precision: Lasers produce highly focused and directional beams, enabling precise applications. High Power: Lasers can deliver high power densities, making them suitable for cutting, welding, and other high-energy processes. Versatility: Lasers can be used for a wide range of applications, from material processing to scientific research. Efficiency: Lasers can be highly efficient in converting electrical energy into light energy. Cleanliness: Laser processes are generally clean and do not require chemicals or solvents.
-
What are the future prospects of laser technology?Laser technology continues to evolve rapidly, with advancements in materials, design, and applications. Future prospects include: Development of more powerful and efficient lasers. Expansion of laser applications in new fields, such as quantum computing and energy production. Miniaturization of laser devices for use in portable and wearable technologies. Increased integration of laser technology into everyday life.
-
What is laser cleaning?Laser cleaning is a non-contact, precise, and environmentally friendly method for removing contaminants, rust, coatings, and other impurities from various surfaces. It utilizes a high-power density laser beam to interact with the contaminant, causing it to vaporize or break down, leaving a clean surface behind.
-
How does laser cleaning work?The laser cleaning process involves focusing a high-power laser beam onto the contaminated surface. The laser energy interacts with the contaminant, causing it to absorb the energy and either vaporize or break down into smaller particles that can be easily removed.
-
What are the advantages of laser cleaning over traditional methods?Laser cleaning offers several advantages over traditional methods, including: High Efficiency: Faster cleaning times compared to manual or chemical methods, leading to increased productivity. Precision: Allows for targeted cleaning of specific areas without damaging the surrounding material. Environmentally Friendly: Eliminates the need for harsh chemicals, solvents, and abrasive materials, reducing waste and pollution. Improved Quality: Provides a cleaner and more precise finish compared to traditional methods. Reduced Costs: Lower operational costs due to reduced chemical usage, waste disposal, and maintenance.
-
What types of materials can be cleaned with laser technology?Laser cleaning can effectively clean a wide range of materials, including: Metals (steel, aluminum, copper, etc.) Plastics Ceramics Glass Wood Stone Composites
-
What types of contaminants can be removed with laser cleaning?Laser cleaning can remove various contaminants, including: Rust Paint Coatings Oil and grease Oxide layers Welding splatter Mold and mildew Graffiti Biological contaminants
-
How do I choose the right laser cleaning system for my needs?Choosing the right laser cleaning system depends on your specific application requirements. Factors to consider include: Material Type: The type of material you need to clean. Contaminant Type: The type of contaminant you need to remove. Cleaning Area: The size and shape of the area you need to clean. Cleaning Speed: The desired cleaning speed and throughput. Budget: Your budget for the laser cleaning system.
-
What are the typical applications for laser cleaning?Laser cleaning has a wide range of applications across various industries, including: Metal Surface Preparation: Preparing metal surfaces for welding, painting, or other processes. Rust Removal: Removing rust from metal surfaces, restoring their appearance and extending their lifespan. Paint Removal: Removing paint from various surfaces, including metal, plastic, and wood. Cleaning of Historical Artifacts: Gently cleaning delicate historical artifacts without damaging them. Industrial Maintenance: Cleaning machinery parts, removing contaminants from tools, and preparing surfaces for repairs. Automotive: Removing rust, paint, and coatings from car bodies, engine parts, and other components. Manufacturing: Cleaning metal parts, removing surface contaminants from molds and dies, and preparing surfaces for welding or painting. Construction: Cleaning concrete surfaces, removing rust from steel structures, and preparing surfaces for coatings. Aerospace: Cleaning aircraft parts, removing coatings from turbine blades, and preparing surfaces for inspection. Medical Devices: Cleaning medical instruments, removing contaminants from surgical tools, and preparing surfaces for sterilization.
-
What is the typical maintenance required for a laser cleaning system?Laser cleaning systems are generally low-maintenance. Regular cleaning of the optics and general inspection of the machine are recommended to ensure optimal performance. Advanced Laser Solutions provides comprehensive support and maintenance services.
-
How can I get more information or purchase a laser cleaning system?For more information, pricing, or to purchase a laser cleaning system, please contact Advanced Laser Solutions directly. You can reach us by phone, email, or through our website.
-
What is laser welding?Laser welding is a precise and efficient welding process that uses a focused laser beam to melt and fuse materials together. It offers several advantages over traditional welding methods, such as high precision, minimal heat input, and reduced distortion.
-
How does laser welding work?In laser welding, a high-power laser beam is directed onto the joint of the materials to be welded. The laser energy is absorbed by the material, causing it to melt. The molten material then flows together, forming a weld pool. As the laser beam moves along the joint, the weld pool solidifies, creating a strong and durable weld.
-
What are the advantages of laser welding?Laser welding offers several advantages over traditional welding methods, including: High Precision: Laser welding allows for very precise control over the weld bead, enabling the joining of very small and intricate parts. Minimal Heat Input: Laser welding uses a highly focused beam, resulting in minimal heat input to the surrounding material, reducing distortion and heat-affected zones. Reduced Distortion: The localized heat input of laser welding minimizes distortion and residual stresses in the welded parts. High Welding Speed: Laser welding can achieve high welding speeds, increasing productivity and reducing manufacturing time. Versatile Applications: Laser welding can be used to weld a wide range of materials, including metals, plastics, and ceramics. Automated Processes: Laser welding processes can be easily automated, enabling high-volume production and consistent quality.
-
What types of materials can be laser welded?Laser welding can be used to weld a wide variety of materials, including: Metals: Steel, aluminum, titanium, copper, brass, nickel, and more. Plastics: Thermoplastics and thermosets. Ceramics: Some ceramic materials can be laser welded.
-
What are the different types of laser welding processes?There are several types of laser welding processes, including: Continuous Wave (CW) Laser Welding: Uses a continuous laser beam to melt and fuse the materials. Pulsed Laser Welding: Uses short pulses of laser energy to melt and fuse the materials. Hybrid Laser Welding: Combines CW and pulsed laser techniques to achieve specific welding characteristics.
-
What are the typical applications of laser welding?Laser welding has a wide range of applications in various industries, including: Automotive: Welding car bodies, engine parts, and other components. Aerospace: Welding aircraft parts, turbine blades, and other aerospace components. Electronics: Welding electronic components, such as circuit boards and connectors. Medical Devices: Welding medical instruments and implants. Manufacturing: Welding various parts and components in different industries. Research and Development: Exploring new applications and materials for laser welding.
-
What are the safety considerations for laser welding?Laser welding involves high-power lasers, so it is essential to follow strict safety protocols: Eye Protection: Always wear appropriate laser safety goggles to protect your eyes from the laser beam. Skin Protection: Avoid direct skin contact with the laser beam. Proper Ventilation: Ensure adequate ventilation to remove any fumes or dust generated during the welding process. Operator Training: Proper training is essential to ensure safe and efficient operation of the laser welding system.
-
What is laser cutting?Laser cutting is a high-precision manufacturing process that uses a focused laser beam to cut through materials. It offers numerous advantages over traditional cutting methods, such as high accuracy, intricate designs, and minimal material waste.
-
How does laser cutting work?Laser cutting involves directing a high-power laser beam onto the material to be cut. The laser energy is absorbed by the material, causing it to melt and vaporize. The laser beam is precisely controlled to follow a predetermined path, creating a clean and accurate cut.
-
What are the advantages of laser cutting?Laser cutting offers several advantages over traditional cutting methods, including: High Precision: Laser cutting allows for very precise cuts, enabling the creation of intricate designs and complex shapes. Intricate Designs: Laser cutting can create intricate designs and patterns that would be difficult or impossible to achieve with traditional methods. Minimal Material Waste: Laser cutting produces minimal material waste, as the cut is very precise and there is no need for additional machining or finishing. Versatile Materials: Laser cutting can be used to cut a wide range of materials, including metals, plastics, wood, ceramics, and fabrics. Automated Processes: Laser cutting processes can be easily automated, enabling high-volume production and consistent quality. Reduced Lead Times: Laser cutting can significantly reduce lead times, as it is a fast and efficient process.
-
What types of materials can be laser cut?Laser cutting can be used to cut a wide variety of materials, including: Metals: Steel, aluminum, brass, copper, titanium, and more. Plastics: Acrylic, polycarbonate, ABS, and other plastics. Wood: Plywood, MDF, and other wood products. Ceramics: Some ceramic materials can be laser cut. Fabrics: Leather, textiles, and other fabrics.
-
What are the different types of laser cutting systems?There are several types of laser cutting systems, including: CO2 Laser Cutting: Uses a carbon dioxide laser to cut materials. Fiber Laser Cutting: Uses a fiber laser to cut materials. Solid-State Laser Cutting: Uses a solid-state laser to cut materials.
-
What are the typical applications of laser cutting?Laser cutting has a wide range of applications in various industries, including: Manufacturing: Cutting metal parts, plastic components, and other materials for various products. Automotive: Cutting metal parts for car bodies, engine components, and other automotive parts. Aerospace: Cutting metal parts for aircraft, spacecraft, and other aerospace components. Electronics: Cutting circuit boards, connectors, and other electronic components. Medical Devices: Cutting metal parts for medical instruments, implants, and other medical devices. Art and Design: Creating intricate designs and patterns in metal, wood, and other materials. Prototyping: Quickly creating prototypes of new products and designs.
-
What are the safety considerations for laser cutting?Laser cutting involves high-power lasers, so it is essential to follow strict safety protocols: Eye Protection: Always wear appropriate laser safety goggles to protect your eyes from the laser beam. Skin Protection: Avoid direct skin contact with the laser beam. Proper Ventilation: Ensure adequate ventilation to remove any fumes or dust generated during the cutting process. Operator Training: Proper training is essential to ensure safe and efficient operation of the laser cutting system.
-
What is laser marking?Laser marking is a non-contact marking process that uses a focused laser beam to permanently alter the surface of a material. It creates marks by either removing material (ablation) or changing its physical properties (color change or surface hardening).
-
How does laser marking work?A laser marking system directs a focused laser beam onto the surface of the material. The laser energy interacts with the material, causing it to either ablate (remove material) or change its physical properties. The resulting mark is permanent and can be a variety of shapes, sizes, and depths.
-
What are the advantages of laser marking?Laser marking offers several advantages over traditional marking methods, including: High Precision: Laser marking allows for very precise and detailed markings, enabling the creation of intricate designs and small text. Permanent Marks: Laser marks are permanent and resistant to wear, abrasion, and chemicals. Versatile Materials: Laser marking can be used on a wide range of materials, including metals, plastics, ceramics, and glass. High Speed: Laser marking is a fast process, enabling high-volume production. Automated Processes: Laser marking processes can be easily automated, ensuring consistent quality and reducing labor costs. Environmentally Friendly: Laser marking is a clean process that does not require any inks, chemicals, or solvents.
-
What types of materials can be laser marked?Laser marking can be used on a wide variety of materials, including: Metals: Steel, aluminum, brass, copper, titanium, and more. Plastics: Acrylic, polycarbonate, ABS, and other plastics. Ceramics: Some ceramic materials can be laser marked. Glass: Laser marking can be used to etch designs or text onto glass surfaces. Wood: Laser marking can create intricate designs and patterns on wood surfaces.
-
What are the different types of laser marking processes?There are several types of laser marking processes, including: Ablation Marking: Removes material from the surface, creating a recessed mark. Color Change Marking: Alters the surface color by changing the material's physical properties. Surface Hardening Marking: Creates a hardened surface area by using the laser energy to modify the material's structure.
-
What are the typical applications of laser marking?Laser marking has a wide range of applications in various industries, including: Manufacturing: Marking parts with serial numbers, barcodes, logos, and other information. Automotive: Marking car parts with identification numbers, logos, and other information. Electronics: Marking electronic components with part numbers, dates, and other information. Medical Devices: Marking medical instruments and implants with identification numbers and other information. Jewelry: Marking jewelry with logos, designs, and other information. Art and Design: Creating intricate designs and patterns on various materials.
-
What are the safety considerations for laser marking?Laser marking involves high-power lasers, so it is essential to follow strict safety protocols: Eye Protection: Always wear appropriate laser safety goggles to protect your eyes from the laser beam. Skin Protection: Avoid direct skin contact with the laser beam. Proper Ventilation: Ensure adequate ventilation to remove any fumes or dust generated during the marking process. Operator Training: Proper training is essential to ensure safe and efficient operation of the laser marking system.

bottom of page